Solving Problems with Torsionally Stiff Couplings
SOMETIMES YOU NEED A FLEXIBLE COUPLING THAT'S TORSIONALLY STIFF
One of our customers in Michigan has a short application story we'd like to share with you. It provides a great example of how precision bellows couplings can help solve machine performance problems.
MICHIGAN CUSTOM MACHINES, NOVI, MI (http://www.michigancustommachines.com/)
Engineer: Brian Nugent
"Michigan Custom Machines builds end of line functional test machines, primarily for the diesel and automotive industries. This particular application required a 400 lb flywheel to mimic the inertia of a diesel engine driveline. The flywheel was mounted to a shaft that needed to be coupled to a custom camshaft which is actuating a fuel injector.

One of the biggest challenges on this application was stiffness of the coupling. We have history with this application and have found if the coupling has wind up, even though it is zero backlash, it will affect how the test is performed by allowing the instantaneous rpm to droop momentarily within part of a revolution.
For this application I called (R+W) direct, also passed information back and forth through e-mail to him. Prior to this application I have always known who R+W was, mainly through word of mouth within the custom test machine community and the internet.
We used a Model BK1/6000/XX. It was a custom model - the adapters were custom to fit the different shaft sizes and the shaft locks we used.
It was known when sizing this coupling, the BK1/6000/XX could not handle as much torque as a previous disc type coupling used, but the stiffness was higher. After installing the BK1/6000/XX, an instrument was used to see how much phase change is seen during operation from one side of the coupling to the other. The BK1/6000/XX showed 1/3 of the phase difference or wind up compared to the previous couplings used. This resulted in more consistent testing of the fuel injector.”
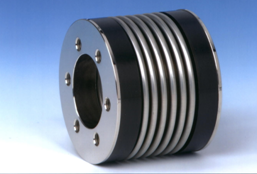
CUSTOM MADE TO FIT
Normally for this 6,000 Nm application we would have worked with our BK3/6000 shaft coupling, but it became clear as we were checking the fits that a special solution would be needed in order to accomodate existing space restrictions. So it was decided that this solution would be based instead on our BK1/6000 basic bellows coupling. One of many custom mounting arrangements we work with here at R+W is to insert special flanges inside the bellows so that keyless locking devices can be used without extending the coupling length. Flat head cap screws allow us to maintain a low profile while still maintaining the structural integrity needed for high torque transmission.
If you have a difficult shaft coupling application you'd like some help with, don't hesitate to contact our applications engineering group at applications@rw-america.com.